Виды сальниковой набивки. Выбор материалов, используемых для изготовления сальниковой набивки. Описание сальниковых уплотнителей
INFLUENCE OF GRAFLEX SEALANTS ON THE ROTARY AND PLUNGER PUMP STUFFING BOX CONSTRUCTIONS
Авдеев В.В., д.т.н., профессор, ген. директор
Ильин Е.Т., к.т.н., доцент, зам. ген. директора по технической политике
Уланов Г.А., главный конструктор
Abstract. The present work observes performance of a pump stuffing box sealant under the environmental and compression forces treatment. Comparison was made berween the interaction of custom sealants and "Graflex" sealants with sealed surfaces. Recommendations were given for stuffing box modification under "Graflex" sealants usage. "Graflex" utilization efficiency was estimated in comparison to the custom sealants.
Наиболее широкое распространение в узлах уплотнения валов центробежных насосов получили давно известные и простые по конструкции мягкие сальниковые набивки . Большинство выпускаемых мягких сальниковых набивок состоит из волокнистой сплетенной основы, пропитанной смазочным материалом с добавками антифрикционных веществ (графита, талька и др.).
Герметичность сальника определяется в первую очередь гидравлическим сопротивлением набивки, оказываемым ею уплотняемой рабочей среде и степенью прижатия ее к уплотняемым деталям . В реальных условиях эксплуатации на сальниковую набивку действует, с одной стороны, усилие затяжки сальника, а с другой стороны - давление рабочей среды, в результате чего происходит пластическая деформация материала и его уплотнение, обеспечивающее снижение пористости и проницаемости.
Вместе с тем, в процессе эксплуатации происходит износ сальниковой набивки, сопровождающийся выносом материала за пределы сальниковой камеры. Герметичность сальникового уплотнения в процессе износа снижается и требует периодического восстановления. Износ материала набивки зависит от ряда факторов, главными из которых являются шероховатость поверхности подвижной уплотняемой детали, вид движения относительно набивки (возвратно-поступательный или вращательный), интенсивность движения, контактное давление набивки на вал, давление уплотняемой рабочей среды, агрегатное состояние и физико-химические свойства уплотняемой среды, прочность внутренних связей материала набивки.
Для восстановления заданной степени герметичности применяется подтяжка сальника. Трудность восстановления герметичности сальника, снизившейся в результате механического износа набивки, путем подтяжки сальника можно объяснить следующим образом. Тонкий слой набивки, прилегающий к перемещающейся уплотняемой детали, подвергается износу и разрушению. Вследствие истирания подвижной деталью пористость материала в этом тонком слое более высокая, чем в остальном объеме набивки. Снижение пористости этого слоя можно было бы осуществлять за счет осевого сжатия и заполнения пустот материалом из основного слоя. Заполнение таких пустот материалом набивки в значительной степени зависит от пластических свойств материала, характеризуемых коэффициентом бокового давления (Кб), который определяет долю осевого усилия приложенного к уплотняющему элементу, передаваемую в радиальном направлении (для большинства традиционно применяемых плетеных набивок типа АП, АС, АПР, АГИ Кб=0,35-0,45). В процессе эксплуатации, при периодических подтяжках сальника, материал набивки уплотняется, теряет пластичность и способность к деформации в осевом и радиальном направлениях. Поэтому приходится прилагать все большее осевое усилие, чтобы обеспечить герметизацию узла, пока не наступит момент, когда обжатие сальника уже не обеспечивает герметичности узла и требуется замена уплотнителя.
К сказанному выше следует добавить, что осевое усилие, приложенное к набивке, существенно уменьшается по глубине сальниковой камеры, в связи с трением набивки о стенки камеры и гильзу вала , а также вследствие внутреннего трения в самой набивке, возникающего при сжатии. В свою очередь сила трения набивки о сопрягаемые поверхности зависит от шероховатости гильзы и стенок сальниковой камеры, а значит и распределение усилий по глубине сальниковой камеры зависит от этих факторов. Так как каждое кольцо набивки вследствие сил трения ослабляет усилие затяжки сальника, то по мере увеличения глубины сальниковой камеры и количества устанавливаемых колец, усилие сжатия последних колец будет снижаться. Снижение усилия обжатия приводит к тому, что слои набивки, контактирующие с рабочей средой, оказываются недостаточно уплотненными, поэтому среда может проникать как через поры самой набивки, так и между штоком и набивкой, приводя к разгерметизации сальника.
Рис. 1. Качественная характеристика распределение радиального давления по глубине сальникового уплотнения.
Ро - осевое давление на сальниковую набивку со стороны нажимной втулки;
Рр - давление рабочей среды;
Рв - давление, оказываемое набивкой на вал.
Качественное изменение радиального усилия на вал по длине сальника, от суммарного действия рабочей среды и воздействия нажимной втулки представлено на рис. 1. Как видно из рисунка, наибольшую нагрузку несут первые кольца, которые в эксплуатации имеют износ составляющий 70% износа всего сальникового уплотнения, в тоже время последние кольца почти не изнашиваются и оказываются по существу лишними. Следует добавить, что крутизна представленной характеристики существенным образом зависит от характеристик материала (от величины коэффициента бокового давления), чем меньше Кб, тем круче будет данная кривая.
Наряду с коэффициентом бокового давления, существенное влияние на величину прижима уплотняемой набивки к гильзе вала оказывает конструкция сальниковой камеры.
Рис. 2. Конструкция сальниковой камеры с промежуточным фонарным кольцом для традиционных набивок.
1. вал насоса;
2. подсальниковое бронзовое кольцо;
3. стенка сальниковой камеры;
4. нажимная втулка;
5. фонарное кольцо.
Большинство существующих конструкций сальниковых камер центробежных насосов выполнено со скосами на торцевой стороне сальниковой камеры и на нажимной втулке, рис. 2. Под действием такого скоса крайние уплотняющие элементы испытывают дополнительное усилие (Ррад), прижимающее их к гильзе вала, рис.3. В результате чего увеличивается радиальное воздействие крайних (первого и последнего) уплотнительных элементов на защитную гильзу вала и их износ возрастает в еще большей степени, причем происходит не только износ уплотняющего материала, но и защитной втулки вала. Практика эксплуатации показала наличие характерных зон износа гильзы вала в районе расположении этих колец. В результате, уже через 0,5-1 год, в зависимости от условий эксплуатации, возникает необходимость ремонта или замены защитной гильзы.
Рис.3. Схема перераспределения передачи осевого усилия от нажимной втулки со скосом.
1.-стенка сальниковой камеры; 2.-нажимная втулка; З.-вал насоса;
Ро - осевое усилие, действующее на нажимную втулку;
Ра - осевое усилие, передаваемое нажимной втулкой на уплотнительное кольцо;
Ррад - радиальная составляющая осевого усилия.
Кроме этого, возникающие чрезмерные радиальные давления могут привести к увеличению трения, местному нагреву вала и даже вскипанию рабочей жидкости и, как следствие, аварийному разрушению сальниковой набивки.
В мировой практике все более широкое применение находят уплотнители на основе терморасширенного графита (ТРГ), экспандированного политетрафторэтилена (ПТФЭ) и их композиты, с применением армирующих высокопрочных волокон. Одним из основных производителей данной продукции в России уже более 12-и лет является НПО УНИХИМТЕК, выпускающее весь номенклатурный ряд уплотнителей под торговой маркой ГРАФЛЕКС.
Основные преимущества новых уплотнительных изделий перед паронитом, асбо-графитовыми кольцами, асбестовыми и хлопчатобумажными набивками определяются тем, что они применимы в широком
(практически неограниченном) диапазоне температур и давлений, имеют хорошие показатели сжимаемости (20-60%) под нагрузкой и восстанавливаемости (10-70%) после ее снятия, упругости (8-12%), не теряют этих свойств со временем - не релаксируют и "не стареют", химически инертны и применимы практически в любых средах, обеспечивают герметизацию уплотняемого узла в течение длительного времени без систематических подтяжек, имеют низкий коэффициент трения 0,02 - 0,12% и высокую теплопроводность.
Наличие перечисленных выше свойств позволяет применять эти материалы для уплотнения подвижных соединений при высоких скоростях скольжения (до V= 25м/с) в широком диапазоне температур и давлений.
В настоящее время для уплотнения насосов ЗАО "Унихимтек" производит уплотнительные элементы в виде колец (КГН-кольца низкоплотные из материала ГРАФЛЕКС) и плетеные набивки (НГФ-набивки плетеные из материала ГРАФЛЕКС). Причем уплотнительные сальниковые кольца изготовляются нескольких типов, витые (КГН-В) и слоеные, различного типа (КГН-СО, КГН-СОП).
Витые кольца изготавливаются путем спиральной намотки графитовой ленты с последующим холодным прессованием в пресс-форме до определенной плотности. В результате такого прессования слои фольги деформируются в виде гофра в осевом направлении и прочно соединяются между собой, обеспечивая герметичность. Плотность прессования колец определяется параметрами и условиями последующей эксплуатации и находится обычно в пределах ρ=0,9-Н,35 г/см³. Эти кольца имеют высокий коэффициент бокового давления (Кб=0,7-0,85), поэтому используются для обеспечения герметизации при малых значениях осевого давления.
Слоеные кольца состоят из чередующихся, горизонтальных слоев графитовой фольги, вырубленных из листа (перпендикулярно оси кольца). Кольцо КГН-СО изготавливается послойной укладкой и склейкой слоев между собой. Кольцо КГН-СОП изготовляется из графитовой фольги с поочередной укладкой каждого слоя и последующей холодной подпрессовкой. Эти кольца обладают высокой теплопроводностью в радиальном направлении λ > 120 Вт/(м К) и низким коэффициентом бокового давления (Кб=0,1-0,15), поэтому используются для отвода теплоты и в качестве дросселирующих. Благодаря малому значению Кб, между валом и кольцом при обжатии сохраняется очень малая щель, где происходит дросселирование потока среды, что обеспечивает более благоприятные условия работы остальных колец.
Плетеные уплотнительные набивки изготавливаются в виде шнура, в основном, квадратного сечения, сквозного, многорядного, диагонального плетения. Нить для плетения получают путем скручивания ленты из графитовой фольги. Для придания прочности плетеной набивке на стадии изготовления фольги производят ее армирование нитями из различного материала (хлопчато-бумажной нитью, стекловолокном, металлической проволокой и другими упрочняющими материалами). Для расширения свойств уплотнительного материала применяются плетеные набивки в комбинации с другими материалами, в частности, с экспандированным фторопластом, высокопрочным волокном - "Кевлар" (СВМ). Для повышения уплотнительных свойств плетеных набивок, а также уменьшения их коэффициента трения и коррозионной активности, применяют пропитку специальными составами и смазками.
Коэффициент бокового давления для плетеной набивки НГФ (Кб=0,5-0,6), в то же время эта набивка имеет достаточно высокий коэффициент теплопроводности, сопоставимый с теплопроводностью металла корпуса насоса.
Разнообразие технологии изготовления уплотнительных изделий из материала ГРАФЛЕКС, позволяет набирать комплекты набивок с заданными потребительскими свойствами.
Рис. 4. Схема сальникового уплотнения вала действующих насосов с комплектацией из уплотняющих элементов ГРАФЛЕКС.
Конструкция узла сальникового уплотнения вала насоса ранее спроектированного заводами-изготовителями для традиционных уплотнительных материалов (набивки из асбестосодержащих, хлопчатобумажных и синтетических материалов с различными видами пропитки) приведена на рис.4а. Глубина сальниковой камеры, как правило, устанавливалась для большого количества колец (6-12 штук), что предопределяет создание большого осевого усилия при обжатии сальника, приводит к росту неравномерности давления на вал в радиальном направлении и быстрому износу крайних уплотняющих элементов. На торцевых поверхностях грундбуксы, подсальникового и промежуточного фонарного кольца выполнены скосы под углом α=15° к торцевой поверхности для улучшения деформации набивки от наружного диаметра к валу.
НПО УНИХИМТЕК, на основании испытаний и опыта эксплуатации таких сальниковых узлов рекомендует применение в качестве уплотнителя плетеную набивку типа НГФ, обеспечивающую длительную и надежную эксплуатацию при минимальных протечках, и увеличении срока службы уплотнения в 2-4 и более раз, в зависимости от условий эксплуатации. При этом конструкция сальникового узла не меняется. В ряде случаев, при наличии в среде абразивных частиц, целесообразно крайние кольца устанавливать из набивки с более прочными нитями, например, из кевлара (СВМ).
Если применение набивок НГФ не обеспечивает желаемых результатов по ресурсу работы, величине протечки рабочей среды или давление среды достаточно высокое Рраб > 2МПа, то это в первую очередь является следствием недостатков конструкции узла сальникового уплотнения вала, компенсировать которые можно путем применения специальных колец из ТРГ ГРАФЛЕКС. Схема комплектации таких узлов приведена на рис.46. Такая комплектация обеспечивает работу уплотнения практически без протечек (величина протечки составляет 1-5 капель в минуту).
Рис. 4б. Схема сальникового уплотнения вала действующих насосов с комплектацией из уплотняющих элементов ГРАФЛЕКС.
Теплоотводящие кольца обеспечивают эффективный отвод тепла как за счет высокой теплопроводности (в сравнении с набивками НГФ и кольцами КГН типа В), так и за счет высокой эффективности дросселирования рабочего давления и выравнивания радиального давления на вал по длине сальника, что приводит к равномерному и более медленному износу сальника.
Для дросселирования большого давления рабочей среды (2 ÷ 4 МПа), а также для рабочих сред со значительным количеством механических примесей, может быть установлено подряд несколько дросселирующих колец со стороны рабочей среды. На рис.4в приведена одна из возможных схем комплектации сальникового узла при наличии фонарного кольца.
Рис. 4в. Схема сальникового уплотнения вала действующих насосов с комплектацией из уплотняющих элементов ГРАФЛЕКС.
Для узла сальникового уплотнения вала насоса, конструкция которого будет разрабатываться для целевого применения комплектов уплотнений из ТРГ ГРАФЛЕКС, мы рекомендуем изменения, представленные на рис.5. Торцевые поверхности нажимной втулки и промежуточного фонарного кольца выполняются перпендикулярно оси вала, без скосов, что позволяет обеспечивать более равномерное распределение радиального давления на вал по длине сальника. Взамен металлических (стальных, бронзовых) подсалышковых колец, устанавливаемых для дросселирования среды с минимальными зазорами по валу δ= 0,2 ÷ 0,3 мм, возможна установка специального дросселирующею кольца из ТРГ "Грфлекс" типа КГН-С. За счет упругости материала, низкого коэффициента трения, высокой теплопроводности и износостойкости дросселирующие кольца долго сохраняют минимальные зазоры, что предопределяет чрезвычайно высокую эффективность дросселирования давления.
Рис.5. Схема конструкции сальникового узла для использования уплотнителей типа ГРАФЛЕКС.
Результаты проведенных исследований показали, что для обеспечения надежной герметизации с использованием уплотнительных материалов ГРАФЛЕКС при давлении рабочей среды до Рр ≤ 1 МПа требуется комплект, состоящий из 3-5 уплотняющих колец, а при давлении рабочей среды выше Рр < 1МПа, целесообразно устанавливать комплект, состоящий из 6 колец.
Кроме этого, благодаря так называемому эффекту "самолечения", заключающемуся в том, что при контакте с уплотнительными изделиями из ТРГ, уплотняемая поверхность покрывается тонким слоем графита, в результате чего происходит заполнение микронеровностей, поверхность становится более гладкой и дальнейший контакт набивки происходит с прографиченной поверхностью, в результате чего коэффициент трения снижается до k=0,02-0,05 (сухое трение ТРГ по стали k=0,l-0,12). Все это способствует уменьшению износа набивки, в результате чего обеспечивается надежная герметичность и долговечность работы уплотнения при меньшем числе уплотняющих элементов.
В свою очередь, сокращение числа уплотняющих элементов позволяет уменьшить габаритные размеры насосов, снизить металлоемкость изделия, сократить затраты на уплотняющие материалы.
Еще больший эффект достигается в процессе эксплуатации у потребителей. Ниже приводятся результаты оценки эффективности применения материалов ГРАФЛЕКС по сравнению с традиционными набивками .
Изменение затрат на материалы за год, в случае замены традиционных уплотнений на основе асбеста на ГРАФЛЕКС можно оценить по выражению:
Где: С асб, С гр - цена асбестового уплотнения и уплотнения ГРАФЛЕКС соответственно, руб/кг;
G асб, G гр - расход материала на сальниковое уплотнение из асбеста и ГРАФЛЕКС соответственно, кг;
η асб, η гр - срок службы уплотнений из асбеста и из материала ГРАФЛЕКС, соответственно, недель;
η год - число недель в году.
В качестве примера, рассмотрим изменение затрат на материалы для центробежного насоса, используемого для перекачки битума на Сызранском НПЗ с учетом реальных сроков службы уплотнений.
ΔS=(0.4·150/2.5-0.4·1350/26)·52=168 руб/год
Таким образом, несмотря на значительно более высокую цену уплотнений ГРАФЛЕКС (С гр = 1350 руб/кг, а С асб = 150 руб/кг), в итоге экономия затрат на материал за год составляет 168 рублей на один насос. Но этим эффективность нового поколения не исчерпывается.
Высокая теплопроводность ГРАФЛЕКС и низкий коэффициент трения позволяют обеспечить работу сальниковых узлов центробежных насосов без протечек перекачиваемой среды через уплотнения (в отдельных случаях предусматривается протечка в пределах 1-5 капель в минуту). Применение обычных набивок требует обеспечения протечки небольшого количества перекачиваемой среды (5-20 капель в минуту (реально еще больше, если среда не является ядовитой)) для предотвращения разогрева сальникового узла, что соответствует утечкам среды около 0,5-1,0 л/час (реально протечки могут достигать 3 л/ч). За год (7000-8000 часов) такие утечки составляют от 4 до 8 тонн продукта. Экономический эффект при этом можно оценить по выражению:
где G пот - утечки перекачиваемой жидкости, т/год;
С пр - цена 1тоны перекачиваемой жидкости, руб/т.
С учетом цены нефти - 3 000 руб/т, эффект от сокращения потерь в этом случае составит от 1.2 000 руб/год до 24 000 руб/год, что практически в 100 раз превосходит затраты на материалы.
Снижение коэффициента трения при использовании уплотнений ГРАФЛЕКС более чем в три раза позволяет получить снижение затрат энергии на привод насоса. Эти затраты также в несколько раз перекрывают расходы на приобретение уплотнительного материала ГРАФЛЕКС. Для современных центробежных насосов механический КПД, который учитывает потери энергии от трения в уплотнениях, подшипниках и дискового трения η м =0,92-0,99. Затраты энергии, идущей на преодоление сил механического трения в сальнике, для традиционных набивок составляют около α с =50% от суммарных механических потерь.
Для этого случая величину снижения потребляемой мощности рассмотрим на следующем примере: для насоса, с мощностью привода N Э =100 кВт замена традиционного сальникового уплотнения на уплотнение из материала ГРАФЛЕКС позволяет на 2/3 сократить потери энергии в сальниковом узле. Если предположить, что исходный механический КПД насоса равен η м =0,95, то в результате получим следующую величину экономии мощности:
ΔN Э =2/3·α c ·N Э =0.667·0.5·0.05·100=1,6675кВт
Казалось бы, ничтожная величина. Однако, при продолжительности эксплуатации насоса τ=7000 часов в год, можно получить экономию электроэнергии:
Э г = 1,6675- 7000 = 11672,5кВт.
При цене электроэнергии 50 копеек, экономия составит S эк.э =5836 рублей. Для сравнения комплект сальниковой набивки на такой насос в среднем стоит около 500 рублей.
Еще больший эффект получается от увеличения срока службы защитной гильзы вала. Опыт эксплуатации показал, что при применении традиционных набивок после одного года эксплуатации необходима либо проточка или, чаще всего, замена защитной втулки. Применение набивок из материала ГРАФЛЕКС позволяет сохранять работоспособность втулки в течение 3-4 лет эксплуатации. Таким образом, экономия от увеличения ресурса защитной гильзы в три раза составит:
С з.в. - цена защитной втулки для данного насоса, руб.;
S p.p. - стоимость ремонтных работ по замене защитной втулки, руб.
Суммарный экономический эффект составит:
Окупаемость уплотнительных материалов ГРАФЛЕКС, как показал опыт эксплуатации, не превышает двух-трех месяцев.
НПО УНИХИМТЕК на базе экспериментальных исследований и опытно-промышленной эксплуатации разработаны и внедрены комплекты уплотнений из материалов ГРАФЛЕКС для действующих насосов, обеспечивающих снижение протечек среды и увеличение срока службы. По результатам теоретических и экспериментальных исследований разработаны рекомендации для внесения изменений в конструкцию сальниковой камеры насоса при использовании уплотнительных материалов ГРАФЛЕКС, обеспечивающих снижение протечек среды, уменьшение износа гильзы вала, расхода уплотняющего материала и снижения затрат на эксплуатацию.
ЛИТЕРАТУРА
- Домашнее А.Д., Хмелъникер В.Л. Сальниковые уплотнения арматуры АЭС. - М.: Атомшдат, 1980, 112с.
- Кришнек Р. Уплотнительные системы на основе графита. Химическое и нефтегазовое машиностроение, № 8, 2000.
- Ворохов A.M., Гашнин А.С., Додо-нов Н.Т. Волокнистые и комбинированные сальниковые уплотнения. М.: Машиностроение, 1966, 312 с.
- Ильин Е.Т. Российские высокоэффективные уплотнения ГРАФЛЕКС - Материалы отраслевого совещания главных механиков нефтеперерабатывающих и нефтехимических предприятий России и СНГ. г. Кириши, 2002, С. 2 59-266.
В промышленном производстве при эксплуатации трубопроводов, различных неизбежно возникают потери перекачиваемых жидкостей. Предупреждению этих случаев служат многочисленные уплотнения, один из которых и будет подробно рассмотрен в данной статье.
Уплотнение сальников насосов
Современное насосное оборудование комплектуется большим количеством элементов. При этом специфика работы требует уделять повышенное внимание нормальному и бесперебойному функционированию изделий в целом. Уплотнение сальников насосов ввиду простоты своей конструкции и легкости применения используется намного чаще остальных уплотнительных устройств.
Эксплуатационные требования
Рабочее колесо всех разновидностей насосного оснащения работает благодаря мотору. Чаще всего он электрический. Через механическую муфту передается энергия от вала двигателя на рабочее колесо, что и приводит его в движение. Сам же вал выходит за пределы корпуса оборудования, что делает оболочку негерметичной. Потому неизбежны потери рабочей жидкости.
Если же использовать то утечки перекачиваемой жидкости можно избежать. Используются следующие технологии:
Набивное (сальниковое) уплотнение. Представляет собой кольцо из волокнистого материала.
Манжетное. Для такого уплотнения применяются эластичные материалы, которые могут быть армированы для увеличения жесткости. Используется для монтажа в насосном оборудовании с малой скоростью вращения вала.
Торцевое. Состоит из двух колец, плотно расположенных друг к другу на валу. Одно из них вращается вместе с валом, а другое остается полностью неподвижным.
Щелевое. Второе название - лабиринтное. Считается самым надежным современным видом уплотнения. Представлено в виде кольца из мягкого сплава. Применяется в многоступенчатых насосах, где использование других технологий может существенно повлиять на КПД.
Помимо этого, существуют приборы, не требующие уплотнений, такие как насосы с магнитной муфтой и мокрым ротором.
Описание сальниковых уплотнителей
Щелевые материалы наиболее часто применяются для обеспечения герметичности погружных насосов. К ним не предъявляются особые требования по утечке жидкостей. Здесь большую роль играет длительность эксплуатации.
Уплотнение сальников насосов появилось практически в одно время с самим оборудованием для перекачки жидкостей. Это своеобразные кольца из волокнистого материала, которые находятся в сальниковой основе, откуда и пошло их название. Набивка должна смачиваться транспортируемой по трубопроводам жидкостью. Это необходимо для охлаждения и смазки сальника. Само же смачивание чревато потерями жидкости. Час работы насоса предполагает потерю 1-15 л воды. Если же набивка не будет смачиваться, то материал потеряет целесообразность использования, быстро «выгорит».
Необходимо постоянно обслуживать сальники. Компрессоры и насосы при этом можно не разбирать, что и является одним из существенных преимуществ уплотнителей. Самообслуживание представляет собой периодическое «подтягивание» манжета.
Типичные вариации уплотнений для насосного оснащения
Современный рынок предлагает различные уплотнения для насосов; типичные сальники представлены двумя основными видами:
Набивка армированная с одной кромкой. Основное назначение - предотвращение потерь перекачиваемой жидкости.
Манжеты армированные пыльником и одной кромкой. Используются для защиты самого соединения от пыли и грязи. Также не позволяют жидкости покидать систему транспортировки.
Если рассматривать то можно выделить сальники:
с формованной кромкой;
с кромкой, прошедшей механическую обработку.
В зависимости от типа используемой резины бывают такие манжеты:
На основе бутадиен-нитрильного каучука. Изделия производятся из 1, 2 и 3 класса резины. Характеризуются относительно высоким порогом отрицательной температуры эксплуатации (-30, -45, и -60 °C соответственно).
На базе фторкаучука. Сырье - резина групп 1 и 2. При перекачке минерального или трансмиссионного масла выдерживают температуру до 170 °C.
Из силиконового каучука. При изготовлении используется резина исключительно 1 группы. Нижняя граница рабочей температуры набивки -55 °C.
Как правило, современные манжеты идут в комплекте с пружинами. Они пригодны для уплотнения на валах разного диаметра.
Пружина может поставляться отдельно от сальника, если предполагается работа с валом до 20 мм или более 120 мм.
эксплуатационные свойства, для каких насосов лучше использовать
Как правило, манжеты отличаются от других уплотнителей своей гибкостью, пластичностью. Высокая износостойкость также является существенным преимуществом изделий. Незначительное воздействие на вал расширяет сегмент применения.
Эксплуатационные характеристики напрямую зависят от структуры уплотнителя и состава, который применялся на производстве. В зависимости от плетения бывают диагональные (сквозные и комбинированные) сальники и одно- многослойные (имеется в виду структура сердечника). По составу манжеты бывают:
асбестовые и безасбестовые;
сухие и пропитанные (в качестве пропитки используются жировые, графитные и клеевые смеси);
армированные и неармированные.
Используются сальники для уплотнения соединения центробежных, и Набивка может применяться и в плунжерном оснащении для перекачки жидкой среды. При монтаже изделия стоит не забывать, что насосы с сальниковыми уплотнениями будут пропускать определенное количество жидкости, упомянутое выше.
Графито-керамические уплотнители
Это один из видов манжетов для насосного оборудования. Применение такого типа уплотнения полностью исключает попадание рабочей жидкости в мотор оснащения. Где же применяются сальники уплотнения графито-керамические? Насосов воды, к которым подходит не так много. Как правило, сегмент применения ограничивается лишь поверхностными механизмами.
Срок службы может достигать 10 лет. При этом стоит придерживаться правильной эксплуатации насосной станции. Основные требования, выдвигающиеся в момент работы оборудования:
Отсутствие «сухого хода». Категорически запрещено держать насос в режиме «вкл», если в системе нет жидкости.
Лучше всего перекачивать максимально очищенную субстанцию. Присутствие примесей сокращает срок службы манжета.
Обязательно нужно придерживаться температурного режима.
Преимущества сальников для насосов с водяным уплотнением
Манжет оборудования для перекачки воды выглядит, как плетеная шнуровка квадратного сечения. Асбестовая (хлопковая или лубяная) нить может иметь включения из медной или латунной проволоки. Сальники насосов с водяным уплотнением имеют сердечник, изготовленный из свинца. Размер ленты 5*0,5. Вместо нее может использоваться плетение из 4 свинцовых проволок.
Применяются сальники с водяным уплотнением, как правило, со стороны всасывания. Но не исключено их использование и с противоположного бока. Размер набивки напрямую связан с диаметром вала. Максимальное число колец уплотнителя - 5.
Как выбрать сальник
Подбор уплотнителей ведется по ряду характеристик. Без сомнений, наиболее важным остается вопрос надежности. Среди прочих, немаловажных критериев рассматривается стоимость. Дополнительные параметры, учитывающиеся при выборе устройств:
количество часов эксплуатации;
потери жидкости;
срок годности;
затраты, которые возникнут в случае ремонта.
Кроме того, подбор уплотнений для насосов осуществляется с учетом типоразмеров. К ним относятся внешний и внутренний диаметры, высота и толщина основы.
Что говорят потребители
Многие уже сталкивались с монтажом сальника для одноступенчатого насоса. Зачастую отмечается универсальность набивки. Использование уплотнителей не ограничивается высокоскоростными валами.
Отмечается, что уплотнение сальников насосов со смазкой на основе силикона проявляет большую термическую устойчивость.
Вариации с высоким содержанием углерода существенно уменьшают степень расширения при увеличении температуры перекачиваемой жидкости. А арамидные волокна со специальной пропиткой из PTFE позволяют сальнику работать в агрессивной среде на химическом производстве, ТЭЦ и в бумажной индустрии.
Сальниковые уплотнения предназначены для герметизации отверстий, через которые проходят или внутри которых размещаются подвижные части механизмов. Нарушение герметичности любого правильно собранного сальникового уплотнения вызывается главным образом потерей эластичности уплотнительных колец (манжет) и односторонним износом трущихся поверхностей деталей. При потере эластичности резко падает усилие, с которым кольцо обжимает шейку вала или прижимается к внутренней поверхности цилиндра, а при одностороннем износе искажается цилиндрическая форма трущихся поверхностей.
Контроль состояния и ремонт деталей. Состояние уплотнитель-ных колец и манжет проверяют обычным осмотром. Во всех случаях при разборке сальниковых уплотнений кольца из войлока, набивку из хлопчатобумажного, асбестового или пенькового шнура или свернутого из этих материалов жгута заменяют независимо от их состояния. Подлежат также замене резиновые кольца и манжеты и самоподжимные сальники, смонтированные в труднодоступных местах механизмов. В остальных случаях резиновые детали и самоподжимные сальники заменяют только при потере эластичности, при наличии надрывов и изъянов на трущихся поверхностях, расслоении или размягчении резины.
Сборка. Любое сальниковое уплотнение нормально работает лишь в том случае, когда сальник обжимает шейку вала или прижимается к поверхности цилиндра равномерно и с одинаковым усилием. Для этого нужно, чтобы оси вала, отверстия детали под сальник и самого сальника были соосными. Кроме того, биение шейки вала, вращающегося в сальнике, должно быть минимальным (не более 0,05 мм), а трущиеся поверхности вала или цилиндра должны иметь гладкую, без заусенцев поверхность.
Уплотнения с войлочными кольцами. Материал и размеры колец любого соединения должны соответствовать требованиям чертежа. Для придания эластичности и уменьшения износа колец их рекомендуется пропитывать в течение 5. 10 мин особыми составами, подогретыми до 120. 130 "С. В качестве таких составов может быть применена смесь из 75 % технического глицерина, 20 % натриевого мыла и 5 % чешуйчатого графита или 90 % касторового масла, 5 % натриевого мыла и 5 % чешуйчатого графита. Кольца, устанавливаемые в крышках, должны входить в выточку крышки плотно. Трущаяся поверхность колец должна быть чистой и ровной, без утолщений, выемок и подрезов, кольцо должно плотно и равномерно обжимать подвижную деталь.
Уплотнения с сальниковыми кольцами. Сальниковая набивка (типа сальника водяного насоса) состоит обычно из отдельных колец с косым срезом. Стыки соседних колец смещают на 120 или 180°. Для ускорения процесса набивки желательно иметь оправки, легкими ударами по которым кольца хорошо уплотняются. Нужно быть внимательным при окончательной затяжке гаек нажимной сальниковой втулки. Неравномерная с перекосами затяжка гаек часто приводит к нагреванию и чрезмерному износу трущихся частей деталей.
Уплотнения с самоподжимными сальниками, резиновыми кольцами и манжетами. В свободном состоянии пружина самоподжимного сальника должна несколько обжимать манжету; усилие обжатия регулируется изменением длины пружины. Слишком большое усилие хотя и повышает герметичность соединения, однако может вызвать перегрев и форсированный износ деталей. Для облегчения монтажа резиновых деталей их трущиеся поверхности смазывают тонким слоем солидола. Чтобы достигнуть лучшего уплотнения, контактирующие поверхности гнезда корпуса и самоподжимного сальника покрывают клеем ГЭН-150В, свинцовыми белилами, герметиком, шеллаком или карбинольным клеем.
Основная часть производства формовых РТИ приходится на уплотнительные устройства, от которых зависит производительность и надежность узлов и механизмов, герметизация и уплотнение стыков, швов и всевозможных соединений. Задача уплотнений – предотвратить или уменьшить утечки жидкости или газа в соединениях деталей машин, трубопроводах и других системах. Уплотнения бывают подвижные, неподвижные, контактные и щелевые. Они могут иметь сложный профиль сечения для обеспечения герметичности и необходимой скорости работы механизма, уменьшения нагрева рабочей жидкости в системе, защиты от проникновения посторонних веществ в техническое устройство и предотвращения наружных утечек рабочей жидкости. В зависимости от химического состава и физических свойств резины уплотнения могут успешно эксплуатироваться в самых разнообразных условиях и применяются во всех отраслях промышленности. К подвижным контактным уплотнениям относятся кольцевые уплотнения, манжеты и другие виды специальных уплотнений. Например, кольцевые уплотнения, изготовленные в соответствии с ГОСТ 9833–73, рассчитаны на надежную работу в гидросистемах при давлении до 32 МПа, в неподвижных соединениях – до 50 МПа. При более высоком давлении рабочей жидкости в системе рекомендуется использование резиновых манжет.
Типы манжет
Обеспечивает герметичность в гидравлических устройствах для машин и узлов (ГОСТ 6969–54, ТУ 38-1051725-86)
Примеры обозначений: Манжета 80х100 Гост 6969-54- манжета для уплотнения цилиндра диаметром 100 мм, штока диаметром 80 мм
Обеспечивает уплотнение зазора между цилиндром и поршнем при давлении от 0,1 до 50 Мпа со скоростью возвратно-поступательного движения не более 0,5 м/с при температуре от – 60С до + 200С (ГОСТ 14896–84, ГОСТ 6969–54). В зависимости от конструкции и значения действующего давления изготавливают трех типов
Примеры обозначений: Манжета 1-20х12-4 ГОСТ 14896-84 - манжета типа 1 для уплотнения цилиндра диаметром 20 мм, штока диаметром 12 мм из резины группы 4
Служит для уплотнения штоков и цилиндров гидравлических устройств, работающих в среде минеральных масел, нефти, пресной и морской воды, водных эмульсий при давлении до 63 МПа при температуре от –50 до +120 °C со скоростью возвратно-поступательного движения до 3 м/с. Эти манжеты устанавливают в комплекте с металлическими опорными и нажимными кольцами (ГОСТ 22704–77)
Примеры обозначений: Кольцо опорное КО 70х95-2 ГОСТ 22704-кольцо внутренним диаметром 70 мм, наружным диаметром 95 мм из резины группы 2
Примеры обозначений: Манжета шевронная М 70х95-2 ГОСТ 22704- манжета внутренним диаметром 70 мм, наружным диаметром 95 мм из резины группы 2
Примеры обозначений: Кольцо нажимное КН 70х95-2 ГОСТ 22704-кольцо внутренним диаметром 70 мм, наружным диаметром 95 мм из резины группы 2
Предназначена для уплотнения цилиндров и штоков пневматических устройств, работающих при давлении от 0,005 до 1 Мпа при температуре от –65 до +150 °C со скоростью возвратно-поступательного движения до 1 м/с (ГОСТ 6678-72). Существуют два типа – тип 1 (для уплотнения цилиндра) и тип 2 (для уплотнения штока)
Примеры обозначений: Манжета уплотнительная 1-025-3 ГОСТ 6678-72- манжета тип 1 для цилиндра диаметром 25 мм из резины группы 3
Примеры обозначений: Манжета уплотнительная 2-010-1 ГОСТ 6678-72- манжета тип 2 для штока диаметром 10 мм из резины группы 1
Для уплотнения вращающихся валов , работающих при более жестких условиях эксплуатации в минеральном масле, воде, дизельном топливе, при избыточном давлении до 0,05 Мпа, температурах от -60 до +170 (в зависимости от группы резины) и скорости вращения до 40 м/с используют манжеты резиновые армированные (ГОСТ 8752–79) . Такие манжеты еще называют сальниками. Эти манжеты армированы металлическим кольцом и круглой пружиной. Металл кольца находится в слое резины, не вступает в реакции с агрессивной средой и укрепляет общую конструкцию, а пружина поджимает рабочую кромку манжеты к валу. Определенные типы манжет могут изготавливаться из фторкаучука и силиконовой резины . Это позволяет применять армированные манжеты в широком диапазоне рабочих параметров при исключительных нагрузках под воздействием самых агрессивных сред.
Изготавливаются двух типов:
I — однокромочные (для предотвращения вытекания уплотняемой среды);
II — однокромочные с пыльником (для предотвращения вытекания уплотняемой среды и защиты от проникновения пыли)
Изготавливаются в двух исполнениях: 1. с механически обработанной кромкой (подрезная); 2. с формованной рабочей кромкой.
Примеры обозначений: Манжета 2.1-60*80-4 ГОСТ 8752–79 - манжета типа 2, исполнения 1, для вала диаметром 60 мм с наружным диаметром 80 мм из резины группы 4
Примечания:
- Буква «С» означает, что пригодность резины для уплотнения данной группы сред определяется по согласованию изготовителя с заказчиком;
- Знак «-» означает, что эластомер неприменим для уплотнения в указанной группе сред.
Все ООО «Харпромполимер» выпускаются в соответствии с ГОСТ 8752-79.
Уплотнения - это приспособления для предотвращения или уменьшения протечки жидкости через зазоры между деталями.
Уплотнения насосов можно разбить на две группы: концевые уплотнения вала (наружные) и внутренние уплотнения ступеней. Концевые уплотнения предназначены для предотвращения утечек перекачиваемой жидкости из насоса и попадания воздуха в насос при его работе с разрежением на входе (сальниковые, торцовые). Внутренние уплотнения предназначены для уменьшения перекачиваемой жидкости между ступенями внутри корпуса насоса в многоступенчатых насосах или между корпусом и вращающимся рабочим колесом в одноступенчатых насосах (щелевые, лабиринтные).
Сальниковые уплотнения (сальник) - это уплотнение вращающегося вала в местах выхода его из неподвижного корпуса, выполненное из мягкой эластичной набивки. Применение сальников в качестве уплотнительного элемента - один из старейших способов герметизации подвижного соединения.
В сальниковых уплотнениях без принудительного поджатия сальниковая набивка укладывается в выточки на неподвижных и подвижных частях соединений. Используется для герметизации подшипников поршней при малых скоростях перемещения и небольшом избыточном давлении.
Сальниковые уплотнения с принудительным поджатием строятся по схеме, в которой герметизация достигается прижатием к валу набивки в результате сжимающего усилия.
В большинстве конструкций сальниковых уплотнений нажимные втулки и грундбуксы изготавливают с наклонной к оси вала плоскостью контакта, что позволяет увеличить радиальное давление уплотнительного давления на вал. Однако чрезмерное увеличение угла наклона приводит к возникновению больших напряжений около нажимной втулки, в результате чего увеличивается износ ближайших к втулке колец.
Поднос воздуха в рабочую полость насоса исключается применением уплотнительного устройства с гидравлическим затвором. Жидкость под избыточным давлением подается в промежуточное кольцо 2. Может подаваться от автономного источника или отбираться из насоса. Таким образом создается гидравлический затвор, препятствующий не только проникновению наружного воздуха в насос, но и предотвращающий утечки перекачиваемой жидкости из насоса. Сальниковые уплотнения с гидравлическим затвором обеспечивают хорошую смазку уплотнительной набивки, сокращая потери на трение в узле и обеспечивая отвод тепла.
Все рассмотренные выше уплотнительные устройства осуществляют поджатие мягкой набивки со стороны, противоположной действию давления перекачиваемой жидкости, т.е. создают максимальное радиальное давление уплотнительного элемента на вал там, где давление перекачиваемой жидкости минимальное.
Рисунок 9 - Сальникове уплотнение с поджатием набивки перекачиваемой жидкости: 1 - внутренняя втулка; 2 - уплотнительный элемент; 3 - подшипник; 4 - наружная втулка; 5 - вал
Лучшие условия работы уплотнения могут быть получены, если обеспечить максимальное радиальное давление элемента на вал там, где давление перекачиваемой жидкости максимальное. Например, уплотняющие устройства, в которых набивка поджимается давлением перекачиваемой жидкости. Поскольку площадь нажимной втулки со стороны жидкости больше, чем площадь со стороны поджатия набивки, создается напряжение, превышающее давление перекачиваемой среды. Такое уплотнение называется дифференциальным.
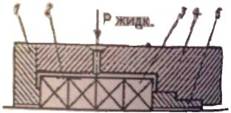
Рисунок 10 - Сальниковое уплотнение с радиальным поджатием: 1 - крышка; 2 - эластичная камера; 3 - уплотнительный элемент; 4 - корпус; 5 - грундбукса.
Равномерного распределения давления набивки на вал можно добиться применением радиального поджатия набивки. В уплотнении с радиальным поджатием набивки между корпусом 4 и уплотнительной набивкой 3 расположена эластичная камера 2, в которую через отверстие подается жидкость под избыточным давлением. Давление жидкости через эластичную камеру равномерно передается уплотнительному элементу, герметизируя соединение.
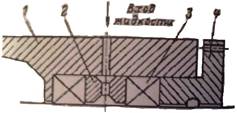
Рисунок 11 - Сальниковое уплотнение с гидравлическим затвором: 1 - корпус; 2 - промежуточное кольцо; 3 - сальниковая набивка; 4 - нажимная втулка
Для повышения долговечности мягкой набивки отдельные ее кольца ограничивают шайбами, которые изготовляют из металла или пластмасс. Уплотнение как бы разбивается на отдельные камеры. Кольца набивки защищены от преждевременного вытекания наполнителя, высыхания и быстрого износа, благодаря чему обеспечивается более длительный срок службы уплотнения.
Основной элемент сальникового уплотнения - эластичная набивка. Материал набивки должен обладать достаточной механической прочностью и упругостью, высокой износостойкостью, непроницаемостью и хорошими антифрикционными свойствами. Согласно ГОСТ 5152-84 различают набивки трех типов: плетеные, скатанные и кольцевые.
Плетеные набивки подразделяют на набивки сквозного плетения и плетения с оплеткой. Для набивки используются хлопчатобумажные, пеньковые, асбестовые, тальковые и синтетические нити. В насосах ЦНС для закачки воды в нефтенасосные пласты используется набивка АГ - плетеная из асбестовой нити пропитанная жировым составом с нанесением графитового порошка, АПР-31 - плетеная набивка из асбестовой нити армированная латунной проволокой пропитанная жировым составом. Ресурс работы таких набивок около 700 часов. Применяются и другие современные материалы с увеличенным сроком службы. Графитированная набивка НГ-Л изготавливается из терморасширенного графита армированная лавсановой нитью. Ресурс работы до 10000 часов.